為了將理論分析的結果與振動測試分析結果對比印證,將測點選在三個箱體軸承座及齒板支承軸孔的上邊緣,如圖6-11所示。
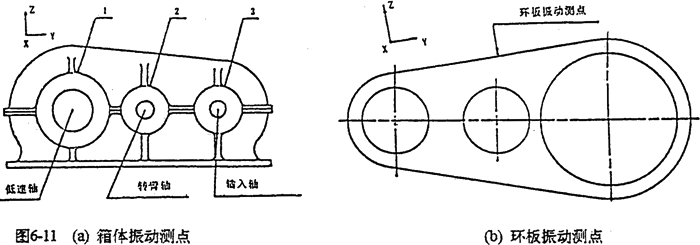
6.4.3實驗步驟
1.跑合試驗
正式試驗之間,減速器在試驗臺上分別以200rpm,300rpm,400rpm,500rpm,…1500rpm空轉,進行20小時的跑合試驗,跑合完畢后更換潤滑油。
2.空載試驗
分別在轉速為800rpm,1000rpm,1500rpm三種空載工況下,測試記錄SHQ40齒板及箱體軸承座上各測點的振動速度及加速度。
3.加載試驗
分別在800rpm,1000rpm,1500rpm等轉速下,測試齒板及箱體軸承座的振動速度及加速度。
6.5 理論計算與實驗結果對比分析
測試結果經頻譜分析處理后,將其與理論計算的結果進行對比分析如下。
1.齒板的振動
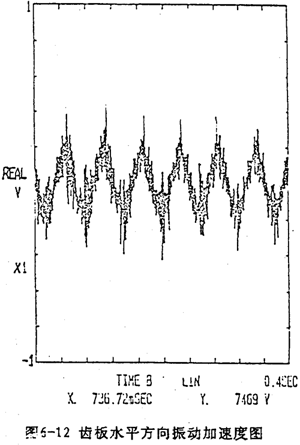
圖6-12是齒板的實測振動加速度時域曲線圖。從時域曲線圖可知,SHQ40型齒板的振動加速度中,存在穩態正弦分量,它是由于齒板作圓周平動運動產生。在其上迭加的每轉兩次沖擊及其振動響應衰減信號,明顯表現出齒板的加速度沖擊信號,而且最大沖擊發生在齒板過死點位置,每轉兩次非等幅沖擊,恰好構成轉頻16.667Hz的周期函數。
經轉換計算后,加速度的最大沖擊值為amax二21844mm/s2。從加速度時或曲線規律發生死點的位置以及最大沖擊值看均與理論計算結果(見圖6-3)相吻合。

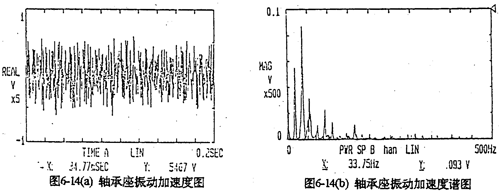
2.箱體軸承座的振動
由于每片齒板都存在同樣的周期性激勵沖擊函數,相位差120°,迭加后的總效果仍然是轉頻周期函數。因此對箱體軸承座的沖擊也呈周期性。圖6-13是支承軸箱體軸承座的振動速度及加速度的實測時域曲線圖。其曲線圖的變化規律及幅值與圖6-4完全接近。速度及速度沖擊值為v
xmax=15.09mm/s,α
max=24960mm/s
2。圖6-14是輸入軸軸承座的實測振動加速度時域曲線及其頻譜分析圖。從加速度譜圖中看出,第一譜峰的頻率值為33.75Hz,恰好是輸入軸轉頻的二倍,也是死點沖擊頻率。死點沖擊是一周兩次,其頻率為33.4Hz,這說明理論計算的結果完全可靠;第二譜峰的頻率值為16.87Hz,與齒板轉頻(輸入軸頻率)相近,是齒板的穩態振動頻率;第三譜峰的頻率值為49.55Hz,是三環減速器的嚙合頻率(50Hz),第四譜峰的頻率值為99.50Hz,是死點的嚙合沖擊頻率。圖6-15是某單齒環內齒行星齒輪減速器的軸承座振動加速度的實測及理論計算曲線圖。從圖可以看出理論和測試的分布規律極為相似。圖中一個周期有一次較大的加速度沖擊峰,是由于行星齒板過180°死點時產生的嚙合沖擊。
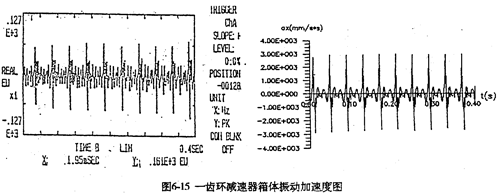
從以上對軸承座的振動實測結果及頻譜分析可知,激勵三環減速器振動的載荷主要有:
(1)平面四桿機構因變形或誤差,在過死點位置時對軸承座產生的沖擊載荷;
(2)齒板作平動圓周運動時產生的穩態動載荷;
(3)齒板與外齒輪之間齒輪副的嚙合沖擊;
(4)平面四桿機構在死點位置時外齒輪造成的沖擊載荷。
3.輸出轉速轉動比
由于機構的變形及誤差等原因,將使輸出轉速及傳動比動變化,沖擊箱體、產生振動。圖6-16是對SHLEO15型三環減速器實測及理論計算的轉速和傳動比隨時間變化的波動曲線。輸出轉速對比為
|
實測結果 |
理論結果 |
最大轉速 |
39.184(rpm) |
39.95754(rpm) |
最小轉速 |
35.358(rpm) |
36.40373(rpm) |
波動量 |
3.837 |
3.55381 |
傳動比對比為
|
實測結果 |
理論結果 |
設計傳動比 |
17 |
17 |
最大傳動比 |
17.556 |
17.580622 |
最小傳動比 |
16.229 |
16.017 |
波動量 |
1.327 |
1.5036 |
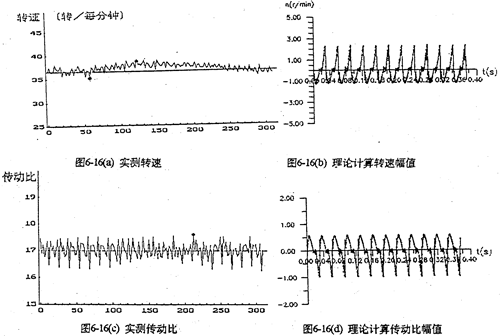
可見,實測值與理論值相近,說明理論計算結果正確。
以上的理論和實驗結果都表明,三環減速器的振動源于平行曲柄機構變形或因誤差產生的死點沖擊。沖擊力大小與載荷成正比,沖擊發生的時間與轉速成反比。功率越大,嚙合力也越大,沖擊峰越高;轉速越高沖擊脈寬越小,激振動力帶寬越寬。因此,減速器在高速重載時,產生的寬帶與較強能量的激振源更容易激發減速器及其附聯結溝的廣泛共振,從而發生強烈振動。特別是推動環板死點的沖擊力矩將可能造成箱體整體及附聯結構的強烈振動。沖擊力還將引起軸、軸承、鍵的較大交變動載,并可能引起鍵聯接的松動、摩擦,發熱等。
通過對SHQ40型三環減速器的理論計算結果及振動實驗的對比研究,說明本文提出的內齒行星傳動的動力分析理論完全正確,可以作為三環減速器等內齒行星傳動裝置的設計分析理論。
6.6控制沖擊振動的方案
前面已從理論和實驗兩方向論證了三環減速器產生振動的根本原因是機構變形及誤差引起的死點沖擊。因此,應從解決死點沖擊出發控制其振動。
1.采用雙軸輸入降低死點沖擊
采用雙軸輸人的齒板及箱體軸承座振動速度、加速度如圖6-17所示。從圖看出齒板速度及加速度值明顯變小(為單軸輸人時的0.3倍),而且無沖擊,完全屬于穩太振動。箱體的振動速度及加速度幅值只是單軸輸人時的0.2倍。圖6-18a是一軸的偏心套存在0.05度的分度誤差時齒板的加速度曲線圖,圖中明顯出現加速度沖擊棒線。采用雙軸輸入后,死點沖擊被徹底(見圖6-18b) , 變成穩態振動曲線了。因此,為了減小三環減速器的振動,有必要加大三環減速器的橫向尺寸,在箱體內增加一套雙軸輸入的齒輪功率分流機構,或者在箱體外另設計一套功率分流機構,以解決機構過死點的振動問題。
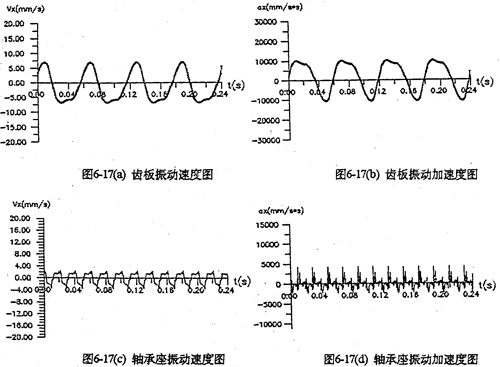
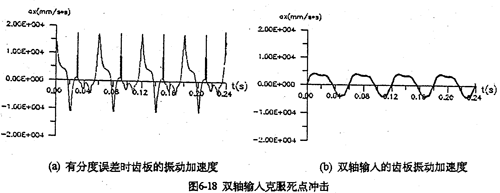
2.改變支承軸的位置
在上一章已經分析過,當三軸水平布置而且高速軸在輸出軸的同側時,載荷幅值最大,各相嚙合力等都很不均衡(見圖5-24)。圖6-19是將支承軸布置在輸入軸與輸出軸間的150°位置時齒板的振動加速度。由圖可知,因誤差引起的沖擊已被完全克服,而且原有的穩態幅值也降低了很多。
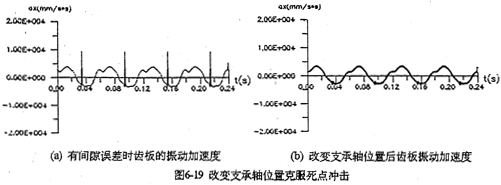
3.增加行星軸承剛度、降低內齒圈剛度
增大行星軸承剛度的目的在于減小雙曲柄機構的變形,降低死點沖擊幅值。并且使各相嚙合力均衡化、減小嚙合沖擊。圖6-20是分別將行星軸承剛度增加一個數量級和內齒圈降低一個數量級時齒板的振動加速度。兩者加速度幅值均降低了1/4倍左右。
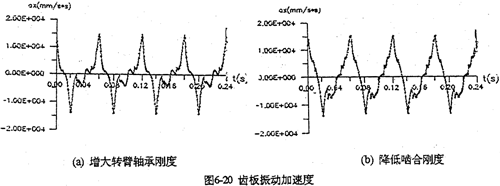
4.減小支承軸或輸出軸的箱體軸承剛度
降低箱體軸承剛度是為了吸收內部機構對箱體的沖擊振動,減小沖擊幅值。圖6-21是轉速為1500(rpm)即時分別將支承軸及輸出軸的箱體軸承與軸之間加一3mm的彈性墊圈時,計算出的箱體振動加速度曲線。從圖中看出,減小支承軸箱體軸承剛度比減小輸出軸箱體軸承的效果更明顯。
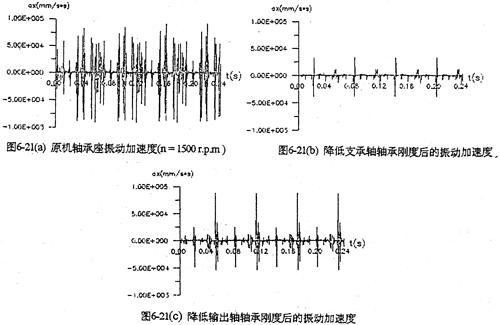
5.增加高速軸的剛度
增加高速軸的剛度是降低沖擊載荷的重要途徑。軸的剛度大(值徑大),扭轉、彎曲變形小,雙曲柄機構變形也就小,這樣既減小了沖擊振動、又增加了軸的強度。圖6-22將高速軸的直徑由原來的45mm加到55mm后的,振動加速度圖。
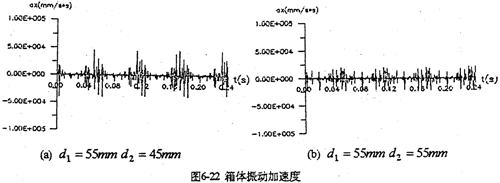
6.對各齒板的死點位置進行修形
由于機構過死點時,因變形要引起死點沖擊,可以通過死點位置及其附近的輪齒(齒板)進行修形,使三相載荷均衡化。圖6-23是將死點位置輪齒修形后,軸承座的振動加速度圖。與圖6-21(a)比較,總體幅值明顯下降。
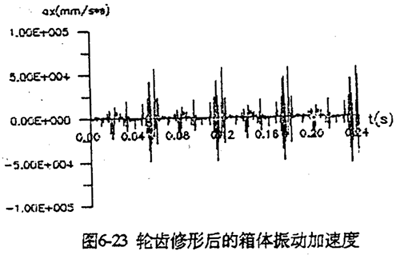
結論
本文對連桿行星齒輪傳動過約束機構的位移協調原理從構件到系統,進行了深入的研究,提出了適合于各種類型的連桿行星齒輪傳動機構的位移協調條件,并建立其動力分析模型,在此基礎上對多次靜不定的過約束機構——三環減速器,建立了包括各種因素在內的動力分析模型,對其動力特性、軸間布置以及振動等問題進行了全面的研究,取得了一系列的成果。
綜合本文的研究成果,其創造性的研究工作體現在以下幾個方面:
●對機構的靜不定次數進行了研究,提出了計算過約束機構靜不定次數的方法。
●研究了機構構件、組合構件的位移協調原理。從系統觀點出發,提出了包括間隙誤差在內的連桿行星齒輪傳動機構的位移協調原理。圓滿地解決了三環減速器等內齒行星傳動過約束機構的動力分析問題。
●提出了一齒環、二齒環、多齒環等內齒行星傳動機構的結構形式。建立了只考慮接觸變形時,在單軸、雙軸及多軸輸入情況下,這些傳動的各種動力分析數學模型,并對常見結構形式的內齒行星齒輪傳動給出了嚙合力、行星軸承載荷等求解的結果,為內齒行星傳動的動力分析計算提供了正確的理論計算公式。
●建立了考慮運動副間隙的內齒行星傳動機構的動力分析模型。
●用有限元的單位載荷法對行星齒板、偏心套進行變形分析,求取其整體變形柔度系數,為內齒行星傳動機構的動力分析準備可靠數據。
●提出了三環減速器的動力分析精確模型,分析了SHQ40型三環減速器的嚙合力、行星軸承載荷、箱體軸承載荷的分布規律。
●研究了影響三環減速器動力特性的各種因素,詳細討論了三環減速器的軸間布置對載荷分布的影響,為改進及優化設計,降低其振動指明了方向。
●從理論上分析了三環減速器產生振動沖擊的機理,提出了描述三環減速器振動的速度、加速度,軸間沖擊角速度、沖擊角加速度,以及輸出轉速、傳動比、輸入扭矩等參數的波動函數。并分析了SHQ40 型三環減速器的振動沖擊特征。
●用實驗研究的結果驗證了理論分析結果的正確性,說明本文提出的理論是完全正確的。
●為降低三環減速器振動沖擊提出了許多可行方案,并從理論上分析了降低振動沖擊的效果。帶誤差、間隙過約束機構的受力分析研究是一個幾乎還沒有人涉及的領域。本文針對含有運動副間隙、構件加工誤差,且具有多次靜不定的過約束機構——連桿行星齒輪傳動機構,考慮機 構構件、組合構件以及機構系統的位移協調條件,推導了機構動力分析方程。利用該動力分析方程研究了三環減速器的動力特性,其結果與試驗研究的結果相吻合,說明該理論是完全正確的。
上一頁